A stronger, more stable and environmentally friendly joining process for ABS sheets: That was the goal of automating the process of assembling engine bonnets for lawn mowers using a collaborative robot. Until now, most projects also used ultrasonics to perform the welds, but they were done manually. With the integration of efficient and reliable ultrasonics welding technology from Herrmann Ultraschall onto a collaborative welding head from ZLIN ROBOTICS s.r.o., this process could be optimized by permanently increasing the process speed and quality in the long term.
Challenge
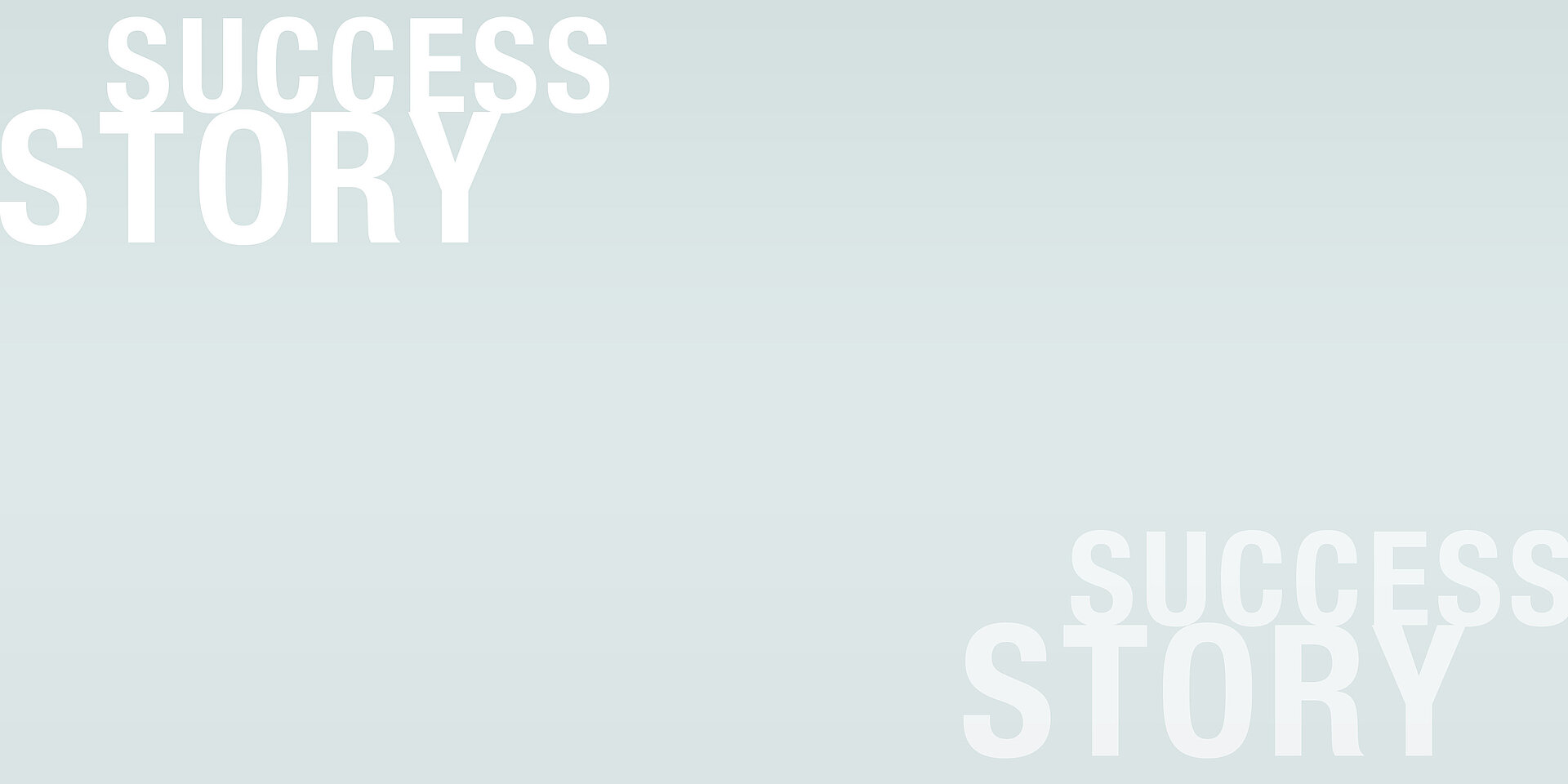
Thermoformed sheets made of different polymer materials like ABS and PC (acrylonitrile butadiene styrene, polycarbonate) are extensively used in many interesting industrial applications. One of them, although maybe not so visible, is their use in bodywork like engine bonnets and roofs of agricultural vehicles, garden machines and lawn mowers, where they replaced old traditional metal and thermoset bodyworks. They look great, weigh less, cost less and allow designers to provide innovative designs.
But these specific materials in new applications and the related need for innovated technologies bring also challenges for many production companies. The manual process of welding with a handheld ultrasonic welder caused many issues concerning process instability and strength of welding points, resulting in unreliable quality and loss of productivity.
Solution
With an automated process, quality and production times can be significantly increased. For this purpose, the ultrasonic stack, which were previously used manually, were installed on a collaborative robot that guarantees a stable and repeatable welding process.
The number of welding per component can be flexibly adapted to the application without having to replace components of the ultrasonic stack. Since the components are joined by spot welds without the use of an energy director, it is also not necessary to change the welding parameters when switching between different applications.
To protect the sonotrode and increase its durability, additional cooling has also been installed.
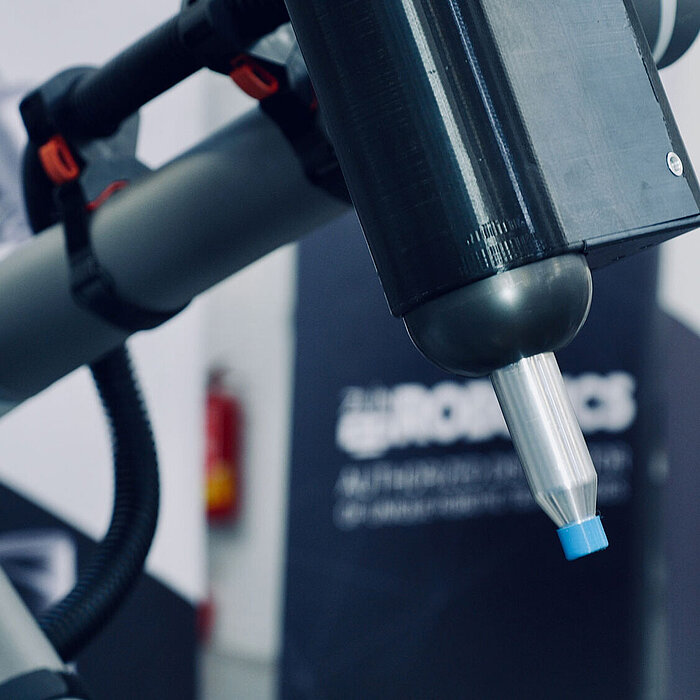
Ultrasonic collaborative welding - lean process in flexible production
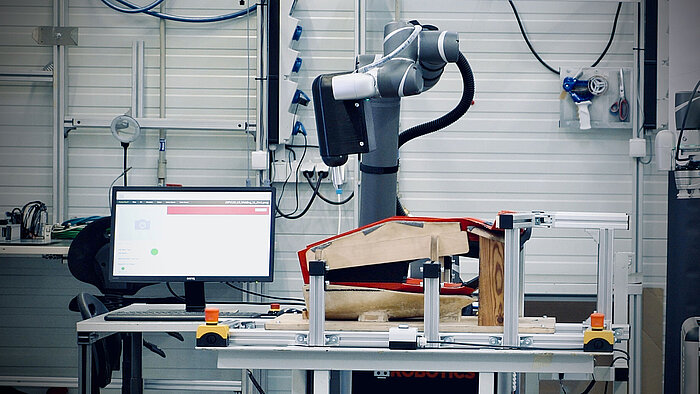
Thanks to the ease of integrating the welding system onto the collaborative robot, ZLIN Robotics was able to automate a previously manual process within a short time. This made it possible to produce consistently high quality and reduce production time.
Together with the use of the innovative collaborative Techman robot, using its camera for optical plane calibration, the user profits from the high flexibility of such a robotic workplace. By using Universal Mobile Stand UMS, which was specially developed for Techman Robot to make it movable, the user can relocate the welding robot to another workplace in less than three minutes.